Compact Integrated Motors
for Decentralized Automation
STXI Motion’s integrated motor solutions combine servo control, drive electronics, and connectivity in one compact unit. Based on low voltage BLDC servo motor technology, these integrated motors are ideal for decentralized machines: simplifying architecture and wiring, reducing cabinet space and maintenance, and increasing design flexibility – with options for Safe Motion, and configurable motor and gear options for optimized fit.
STXI Motion’s integrated motor solutions combine servo control, drive electronics, and connectivity in one compact unit. Based on low voltage BLDC servo motor technology, these integrated motors are ideal for decentralized machines: simplifying architecture and wiring, reducing cabinet space and maintenance, and increasing design flexibility – with options for Safe Motion, and configurable motor and gear options for optimized fit.
Ideal Applications for Integrated Motors
Segments such as intralogistics, packaging, food & beverage, printing and textile manufacturing are increasingly adopting modular, decentralized drive systems. These benefit from space-saving designs, reduced wiring, and the integration of advanced servo motors with integrated drive technology.
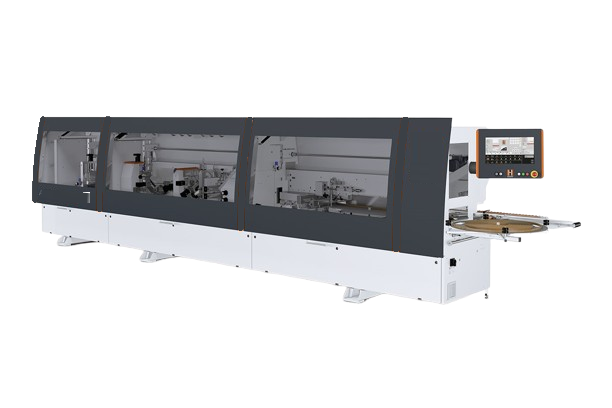
Multiple Axis or Long Machines
These setups offer significant potential for reducing wiring, cabling, and installation effort. By eliminating bulky control cabinets, compact servo motors minimize footprint and simplify machine layout.
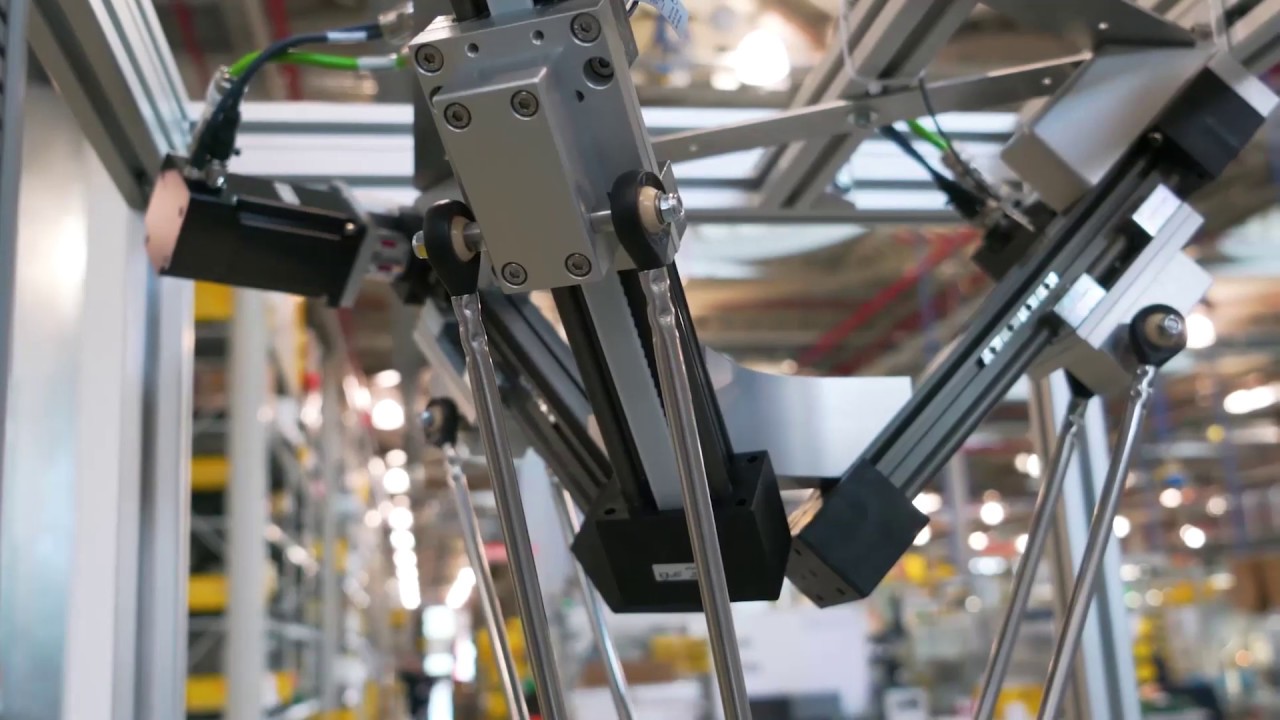
Direct Mount
Motors
In applications like rotary tables or cartesian systems, where motors must move with the axis, compact integrated servo motors help minimize cabling. This reduces mechanical complexity, limits wear and eliminates common failure points.
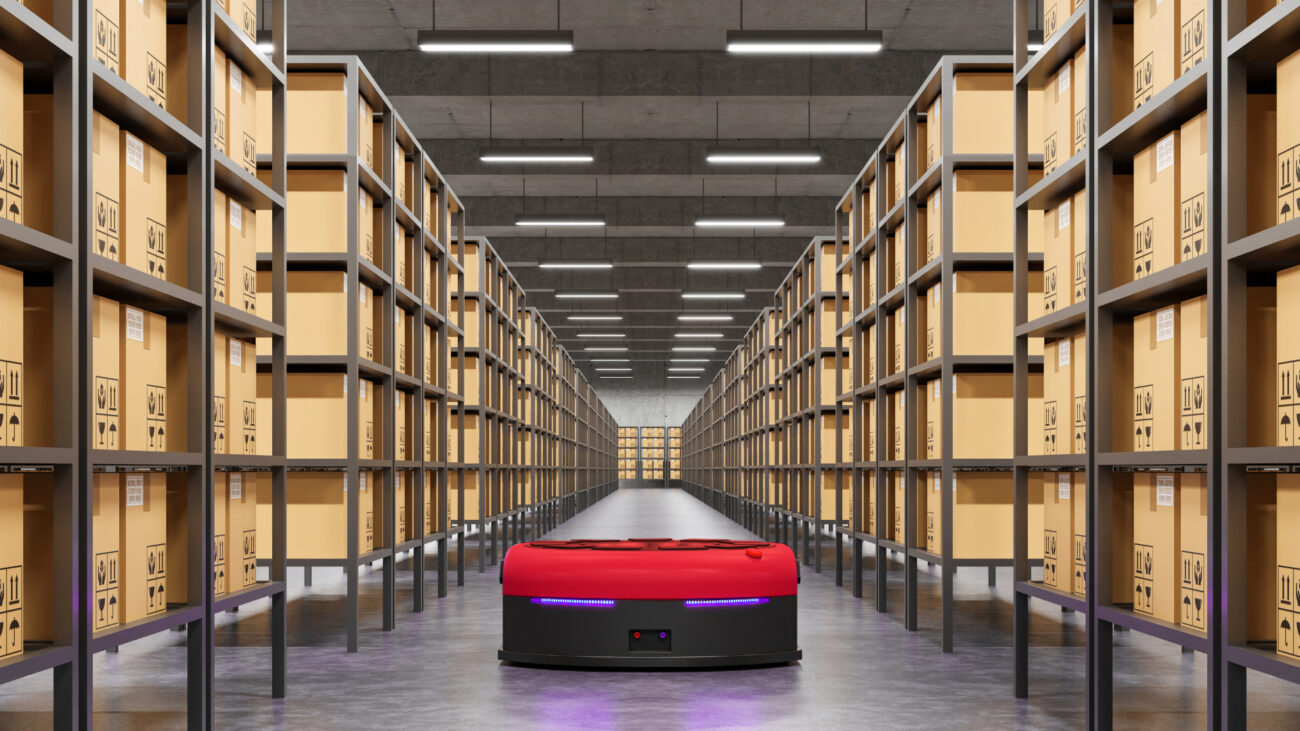
Mobile/ Battery
Powered Systems
In AGVs, AMRs, AS/RS and shuttle systems, space is limited and efficiency is key. Low voltage motors with certified Safe Motion ensure safe, robust performance even in challenging environmental conditions.
Key Benefits of Decentralized Drive Solutions
Less cabling
& installation
effort
Integrated motors reduce wiring, speed up setup and minimize wear.
Space-saving
design
Compact, all-in-one units eliminate the need for external drives and cabinets.
Greater
flexibility
Modular, decentralized setups allow quick adaptation to machine layouts.
Higher
efficiency
Optimized low-voltage architecture boosts system performance and reliability.
Haaave you met
?
TIM is a compact integrated servo motor that eliminates control cabinets, cuts wiring, and frees valuable machine space. 48–60 VDC low-voltage power, Functional Safety-certified Safe Motion Module, and CANopen or EtherCAT connectivity come built in – so you install one unit and get drive, control, and safety in a single package.
Result: faster commissioning, lower total cost, and reliable performance in every decentralized machine.
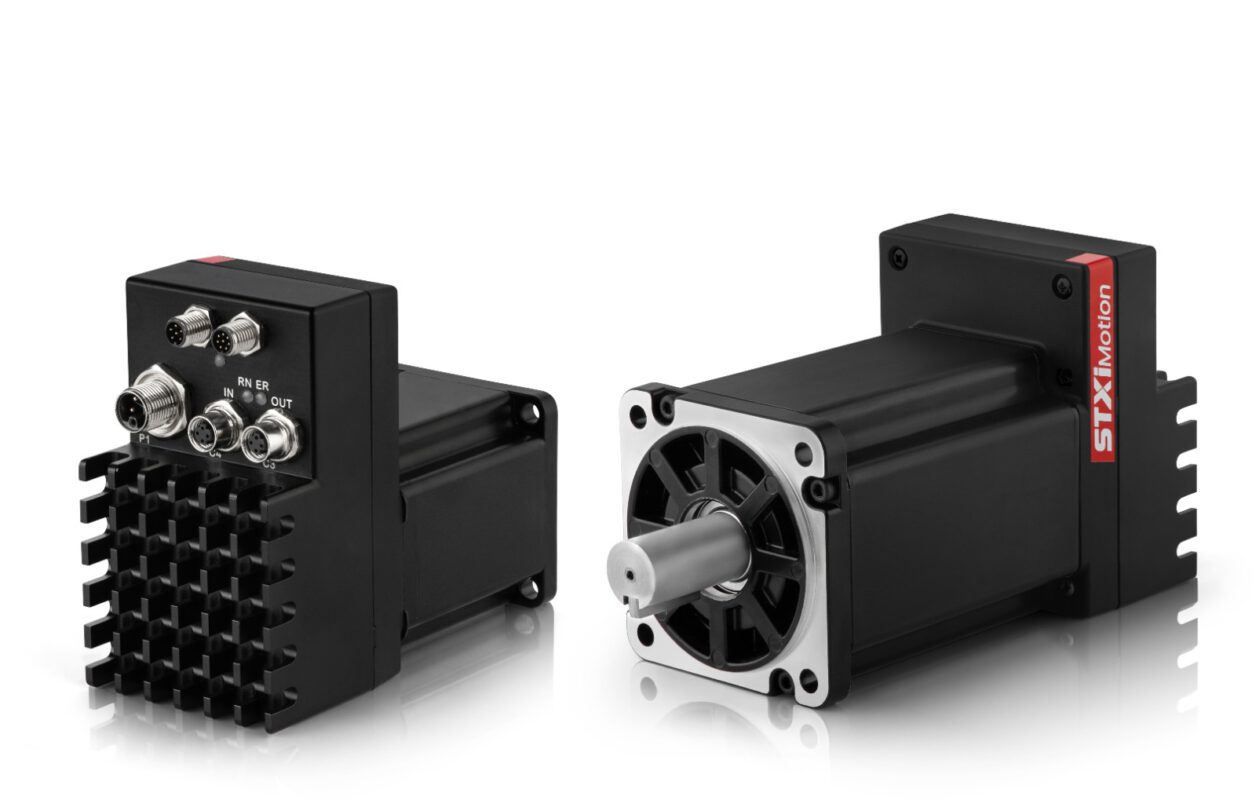
Integrated Functional Safety-STO or optional Safe Motion Module (Cat 3, PL e)
Integrated servo
electronics
Flange size: 60, 80 mm
With/without brake
Feedback: absolute single turn/absolute multi turn
STO
I/O: 3 IN, 1 OUT
Fieldbus: EtharCAT, CANopen
SAFE
MOTION
MODULE
Safety Enhanced, Performance Uncompromised
The optional Safe Motion Module adds certified drive-based safety functions to TIM integrated servo motor – beyond standard STO and SBC. Fully compliant with IEC 61800-5-2, it enables advanced safety features like Safe Stop, Safe Limited Speed, and Safe Direction – directly on the drive.
Safety over EtherCAT (FSoE) streamlines integration with a single cable – ideal for mobile robots and other space-limited systems. Result: less wiring, more safety, faster implementation.
Safe Motion Module supported functions:
Safe Torque Off (STO)
Safe Stop 1 (SS1‑t, time-controlled)
Safe Stop 1 (SS1‑r, ramp-monitored)
Safe Stop 2 (SS2‑r, ramp-monitored)
Safe Operating Stop (SOS)
Safely Limited Speed (SLS)
Safe Brake Control (SBC)
Safe Brake Test (SBT)
Safe Speed Monitor (SSM)
Safe Direction (SDI)
All functions conform to IEC 61800-5-2, with safety communication through the FSoE protocol, compliant with IEC 61784-3:2021.
SAFE
MOTION
MODULE
Safety Enhanced,
Performance Uncompromised
The optional Safe Motion Module adds certified drive-based safety functions to TIM integrated servo motor – beyond standard STO and SBC. Fully compliant with IEC 61800-5-2, it enables advanced safety features like Safe Stop, Safe Limited Speed, and Safe Direction – directly on the drive.
Safety over EtherCAT (FSoE) streamlines integration with a single cable – ideal for mobile robots and other space-limited systems. Result: less wiring, more safety, faster implementation.
Safe Motion Module
supported functions:
- Safe Torque Off (STO)
- Safe Stop 1 (SS1‑t, time-controlled)
- Safe Stop 1 (SS1‑r, ramp-monitored)
- Safe Stop 2 (SS2‑r, ramp-monitored)
- Safe Operating Stop (SOS)
- Safely Limited Speed (SLS)
- Safe Brake Control (SBC)
- Safe Brake Test (SBT)
- Safe Speed Monitor (SSM)
- Safe Direction (SDI)
All functions conform to
IEC 61800-5-2, with
safety communication through the FSoE protocol, compliant with IEC 61784-3:2021.